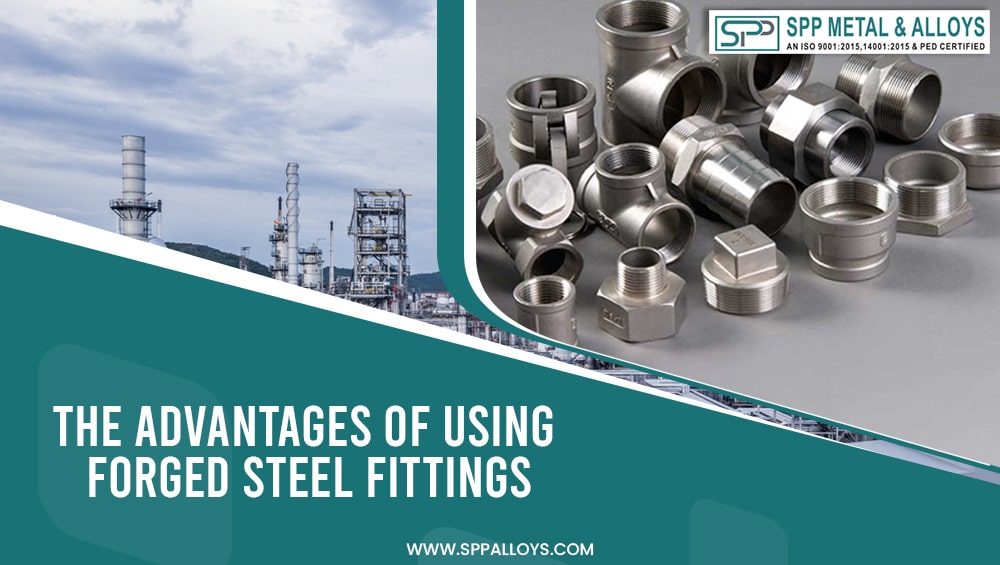
The Advantages of Using Forged Steel Fittings in High-Pressure Applications
Forged fittings play a crucial role in many industrial applications, especially in high-pressure systems. These fittings are made by forging or shaping metal bars or billets into the desired shape. Forged fittings offer several benefits over traditional welding or casting methods, making them a preferred choice for high-pressure applications.
In this article, we will explore the applications and benefits of high-pressure forged fittings, including the materials used, their construction, and the different types available.
What is High-Pressure Forged Fittings?
High-Pressure Forged Fittings are a type of pipeline fitting that is designed to withstand high levels of pressure in industrial applications. These fittings are typically made from high-strength materials such as carbon steel, stainless steel, or alloy steel and are commonly used in the petrochemical, oil, and gas, and power generation industries.
Types of High-Pressure Forged Fittings
There are several types of high-pressure forged fittings, each designed for specific applications. Some of the most common types include:
- Elbow fittings
- Tee fittings
- Coupling fittings
- Cross fittings
- Union fittings
- Cap fittings
- Plug fittings
- Nipple fittings
Each type of fitting offers its own set of advantages, depending on the application. For example, elbow fittings are commonly used for connecting pipes at a 90-degree angle, while tee fittings are used to split a single pipe into two.
Materials Used in High-Pressure Forged Fittings
The materials used in high-pressure forged fittings must be strong and durable, able to withstand the high pressures and temperatures of these applications. Some of the most common materials used include:
- Carbon Steel
- Stainless Steel
- Alloy Steel
- Duplex Steel
- Nickel Alloys
Each material offers its own unique benefits, including resistance to corrosion, high strength, and durability.
Grades of Forged Fitting
- Super Duplex: S32750/S32760/F55/F53
- Duplex: S31803/S32205/SMO 254
- Nickel Alloys: Alloy 400, 625, 800, 825
- Stainless Steels: 304, 316L, 321, 310S, 904L, etc
- Carbon Steel: A105
- LTCS: LF2
- Alloy Steel: F9/F11/F12/F22/F91
Manufacturing of High-Pressure Forged Fittings
High-pressure forged fittings are manufactured through a process called forging, which involves heating metal bars or billets to high temperatures and then shaping them into the desired shape. This process results in fittings that are stronger and more durable than those made through casting or welding methods.
Forged fittings are typically made in one piece, which eliminates potential weak spots and leaks in the connection. They are also tested to ensure that they meet industry standards for strength and durability.
Benefits of High-Pressure Forged Fittings
The benefits of high-pressure forged fittings include:
- High Strength: Forged fittings are made from strong, durable materials and are manufactured through a forging process, making them stronger and more durable than fittings made through other methods.
- Leak-Proof Connections: The one-piece construction of forged fittings eliminates potential weak spots and leaks in the connection, ensuring a secure and leak-proof connection.
- Cost-Effective: Forged fittings are more cost-effective than welded fittings in the long run, as they require less maintenance and have a longer lifespan.
- Easy to Install: Forged fittings are typically easier to install than other types of fittings, as they do not require welding or other complex methods.
- Versatile: Forged fittings are available in a wide range of sizes and types, making them suitable for a wide variety of applications.
Applications of High-Pressure Forged Fittings
High-pressure forged fittings are used in a wide range of industries and applications, including:
- Oil and gas
- Power generation
- Chemical processing
- Water treatment
- Mining, and many more.
In these industries, high-pressure forged fittings are used to connect pipes and transfer fluids and gases at high pressures. They are also used in high-temperature applications, where their strength and durability are essential.
Conclusion
High-pressure forged fittings offer a range of benefits over other types of fittings, making them a preferred choice for many industrial applications. Their strength, durability, and leak-proof connections make them ideal for high-pressure and high-temperature systems. The versatility of forged fittings, combined with their ease of installation and cost-effectiveness, make them a top choice for industries such as oil and gas, power generation, chemical processing, water treatment, and mining.
Whether you are in need of elbow fittings, tee fittings, or any other type of high-pressure forged fitting, it is important to choose a reputable supplier that offers quality products and reliable customer service. By investing in high-pressure forged fittings, you can ensure that your industrial operations run smoothly and efficiently.